The supply chain industry is quickly becoming the breeding ground for some of the most modern technological advancements of this century and can be characterized as a hyper-transformation industry. Warehouses are at the epicenter of distribution in the supply chain and face arduous obstacles in maintaining continuous efficiency, safety, and managing volume.
Key Drivers in the Evolution of Warehouse Automation
Consumer demand is climbing higher every day because of the sheer buying agility that consumers now have. Mobile technology and the Human Computer Interaction field has generated seamless user experiences that are accelerating growth in the e-Commerce space. Companies such as Amazon are leading the pack in meeting the rising demand of consumers, and retailers are making a mad dash to grab hold of end-to-end transformation initiatives to gut legacy systems and compete in the modern digital age.
This massive push to compete with consumer demand has naturally grown the need to scale warehouses and expand volume. In the year 2000, the average size of warehouses was approximately 65,000 square feet. In 2017 the average square footage grew to about 181,370 square feet. Growth in warehouses could also mean more locations versus adding on to a single site. 28% of distribution centers doubled the number of buildings they had between 2016 and 2018 to meet increasing consumer demand.
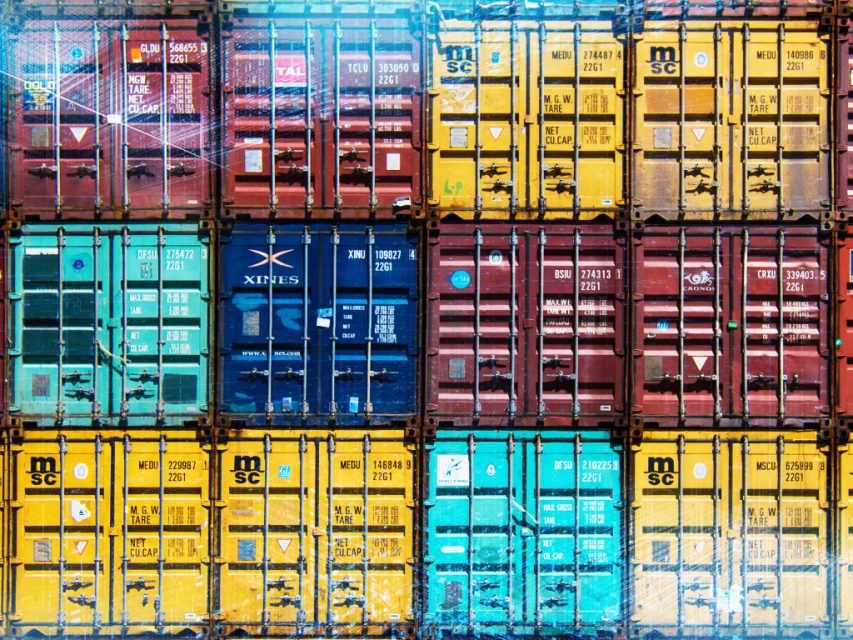
Trends That are Impacting the Supply Chain Industry
Current global trade conditions are creating a tumultuous environment for the supply chain industry because of many businesses that have full operations overseas or import supplies that are needed for products. With current tariffs on the rise and an ongoing trade war with no end in sight, companies are forced to either reroute supplies, raise prices or absorb costs. Managing inventory levels and margins becomes mission-critical in this climate as inventory mistakes can add to the already soaring costs that businesses are facing.
Robotics is a critical driving force in warehouse automation. Autonomous Mobile Robots are providing companies with both speed and accuracy in handling materials. Merging robotics and AI technologies is growing the capability of current operator reliant robots. Research predicts that the number of robots in warehouses will increase by at least 15 times by the end of 2021.
Machine learning is continuing to evolve and play a significant role in warehouse automation. Its design uses advanced algorithms to find system anomalies, moderate inventory, and find meaningful use in large data sets to optimize performance. The benefits that machine learning has added to the supply chain arena is vast, and companies are utilizing it not only for day to day operations but also to recognize parallel collaboration synergies among multiple shipper networks.
Picking has been a significant pain point in distribution centers, especially for grocery based companies. Manual picking has declined 4% from 2019 due to robotic technology becoming smarter and more capable of filling orders on their own. A goods-to-person system is a prominent solution that many distribution centers already employ. This process becomes more complex as the number of SKUs grows, but this process still reduces travel time for employees.
The warehouse automation boom is skyrocketing, and the tools, software, and hardware needed to perform are leading the industry at the pinnacle of innovation. Warehouse automation is projected to be a $27 billion industry by 2025, and it’s predicted that the logistics automation industry will reach $107.84 billion in the same year.
Cloud-based inventory tracking tools are providing teams with real-time data and can be easily accessed by distribution center floor associates for smooth coordination of supply-and-demand. The ability to track inventory in the cloud has reformed the data collection process so that it’s not individual workers transposing SKUs, but those same workers operating a barcode scanner that automatically translates the data to the cloud-based inventory software in the previous point.
SKUs are growing exponentially in warehouses, but more SKUs can be processed using automated solutions. In 2018, the average number of SKUs in a warehouse reached 13,985, which is an increase from 13,130 SKUs just last year. Flexible systems with modular components are meeting the rapid growth of SKUs, and complete storage solutions are now able to process shipments faster and with more accuracy.
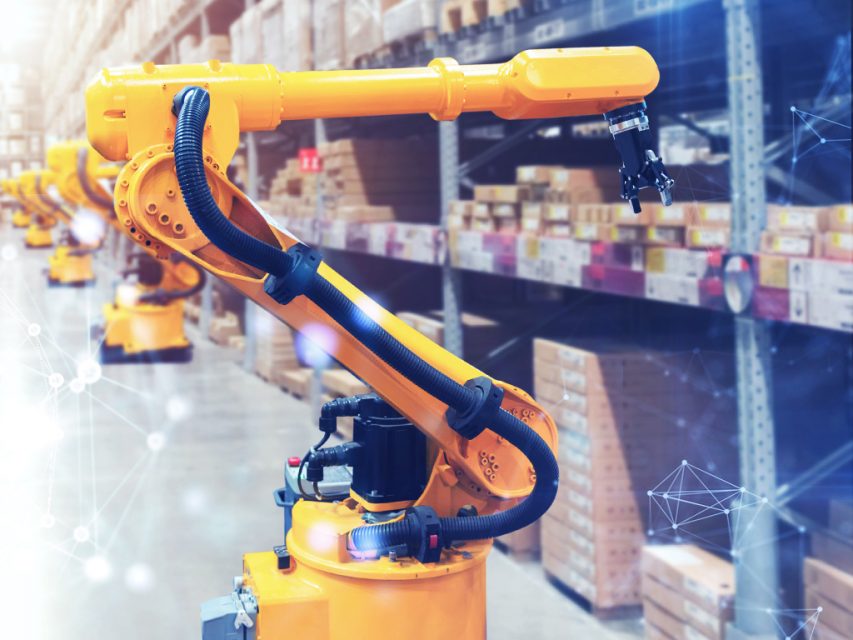
Conclusion
As warehouses continue to expand and become more automated, workplace conditions and safety measures must also scale. Simple solutions such as two-way radios or cellular devices with GPS and emergency features can be easily assigned to each employee. This would allow employees movements to be tracked so that tasks can be assigned based on location.
This simple shift saves time and reduces wear and tear on employees that walk up to 10-15 miles per day in large warehouses. Two-way radios are also safety mechanisms that employees can use to request immediate assistance in the event of an injury, and instantaneous communication can be established between employees and supervisors in case of an emergency.